Cover Story
What is 3D printing adding to manufacturing and maintenance?
3D printing has been embraced by the rail industry over recent years. Keri Allan explores why rolling stock constructors and maintenance companies are keen on the use of additive manufacturing.
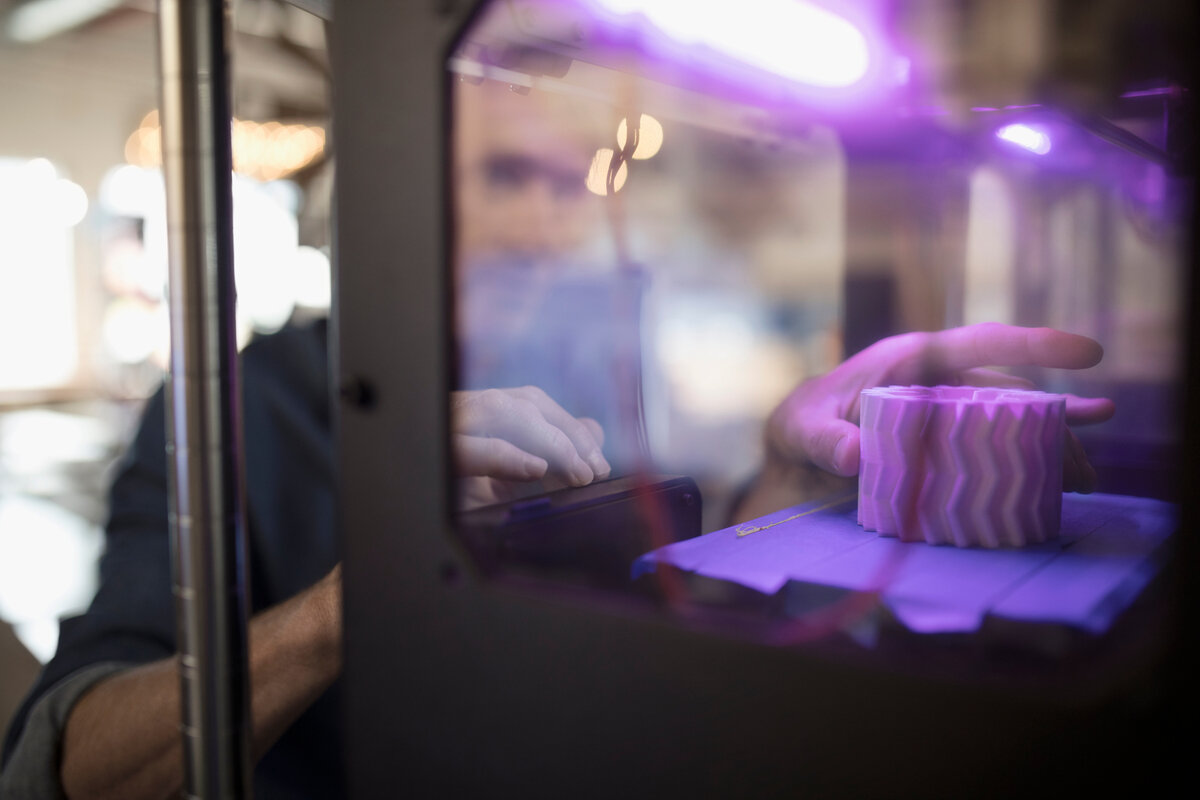
Render of the West Yorkshire mass transit system tram passing through Leeds City Centre. Credit: West Yorkshire Combined Authority
3D printing, also known as additive manufacturing, is revolutionising the rail industry. First used for producing small quantities of hard-to-find spare parts, it’s now used to create a wide range of complex components in large volumes, transforming manufacturing processes across the sector.
The technology is well suited to the demanding environment of the rail industry thanks to its ability to create highly customised parts in a range of materials, from carbon-reenforced flexible polymers through to various metals, including aluminium and titanium.
Today, it’s used to produce anything from spares and interiors to exterior panels, and it’s been embraced by many of the industry’s big players. This includes Hitachi Rail, which recently purchased Argo 500 3D printing systems from Roboze to make spare parts for its rolling stock from reinforced carbon fibre and resin.
Another example comes from Siemens Mobility, which has over 50 3D printers across more than 16 of its sites globally and has designed and produced components for over 100 customers.
“We started with 3D printing over 10 years ago to solve obsolescence problems for spare parts,” says Christian Ochs, head of additive manufacturing Siemens Mobility. “Over time, it’s been used more and more to enhance the design and shorten lead times of rail spare parts as well as for serial production high-end components for new railway systems.”
Ochs notes that Siemens uses 3D printing to produce a wide range of applications, from repair parts like overhead luggage rack supports to newly designed items. These have included the lightweight air conveyance ejectors for the Mireo and Desiro trains’ water tanks and optimised nozzles for sanitary systems on Amtrak Intercity trainsets (ICT).
Using 3D printing in rolling stock maintenance
“Initially, 3D printing was predominantly used for rapid prototyping, allowing manufacturers to quickly iterate and refine designs,” says Jessica Di Toto, operational technology engineer, Hitachi Rail. “However, with advancements in technology, we are now able to produce end-use components that meet the stringent requirements of the rail sector.”
At present, one of the main use cases for 3D printing is rolling stock maintenance, where it’s being used to quickly produce – often obsolescent – parts and help operators reduce vehicle downtime, and the corresponding penalty and retention payments.
“It tackles the challenge of obsolete parts, allowing the production of replacements for components no longer readily available, and jigs and tooling can be tailored for specific depot needs,” says Ross Nicholls, technical director of 3D printing service provider Malcolm Nicholls.
The ability to produce parts on-demand helps address the challenges of maintaining and servicing ageing rolling stock.
Gavin John Lockyer, CEO of Arafura Resources
“It also enables the rapid production of replacement parts, minimising downtime and keeping trains running on schedule, and eliminates the need to wait for parts to be shipped. This is a major advantage when dealing with legacy equipment or custom components.”
Ochs adds that maintenance efforts can be further reduced by 3D printing new tools and fixtures as well as redesigning and printing more durable parts and reducing assembly time by functional integration.
“The ability to produce parts on-demand helps address the challenges of maintaining and servicing ageing rolling stock, where certain parts may no longer be available through traditional supply chains,” adds Di Toto. “Rare or obsolete parts are readily available, helping to keep older trains in service without unnecessary delays.
“What’s also exciting is the potential for rapid iteration. If a part consistently encounters issues, we can quickly redesign and produce a new version, incorporating feedback from our maintenance teams. This ability to rapidly improve and refine parts leads to greater reliability and can spark innovations that benefit the entire fleet.”
Time and cost savings
“The decision to explore 3D printing stemmed from the need to innovate within the constraints of traditional manufacturing. The rail industry is characterized by long lead times, the necessity to maintain large inventories, and the challenges of managing obsolescence,” explains Di Toto.
This highlights one of the biggest benefits to come from embracing 3D printing – time savings. Last year Simran Sandhu, Alstom UK and Ireland’s senior procurement manager, oversaw the installation of 3D printers at the company’s main UK base in Derby. She has since seen a big improvement in the quick resolution of any jigs and tooling that are required, often during new build production.
“Instead of waiting for these parts to be supplied by external parties on a 10-20-week lead time, they can now be printed in one or two days on site. Ultimately, this contributes to a much more time-efficient and smoother production line,” she says.
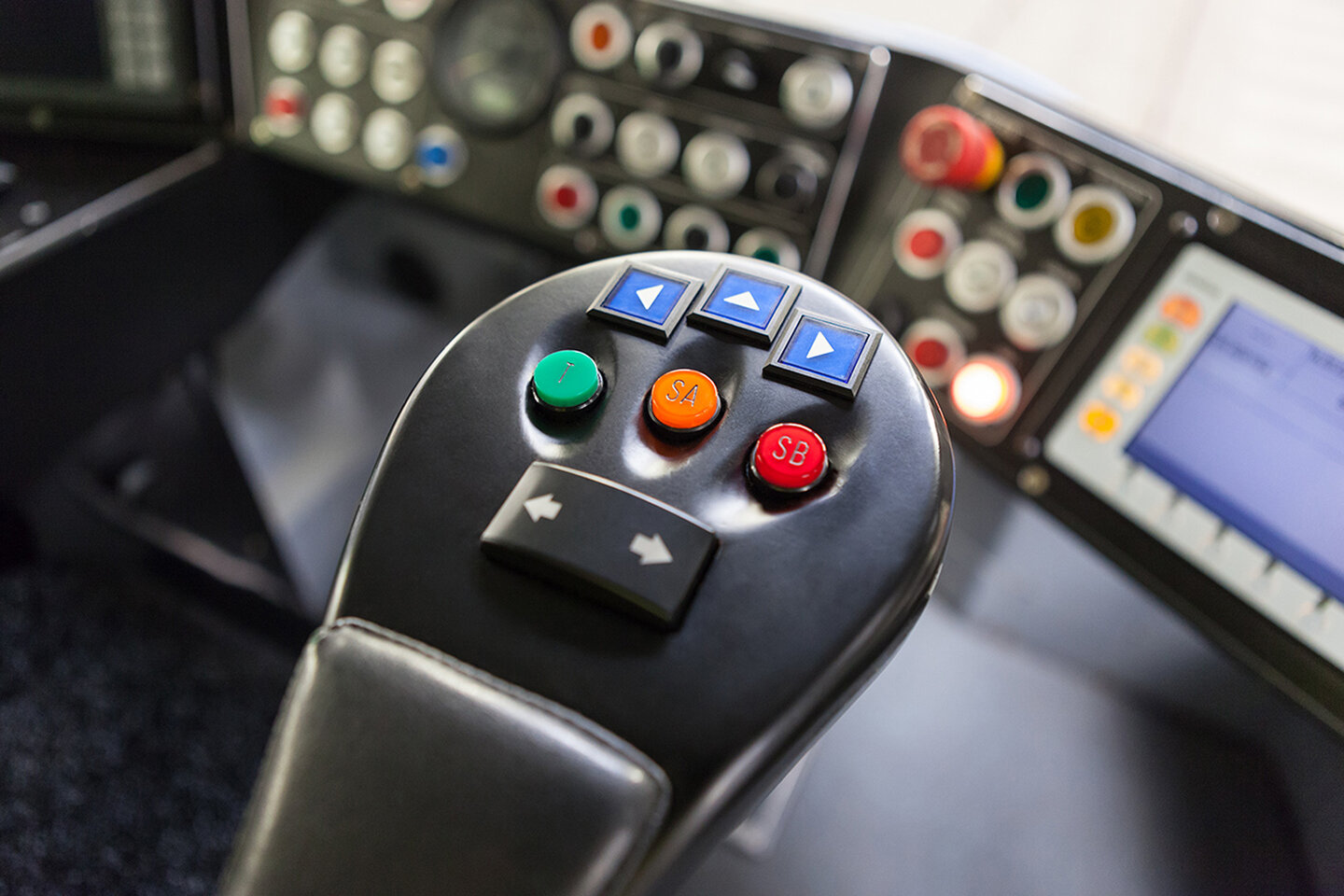
A driver seat armrest produced by Siemens Mobility with the assistance of 3D-printing technology. Credit: Stratasys
The cost savings also cannot be overlooked, with Ochs noting that users no longer need to purchase any expensive molds or tools, and material waste can be reduced by up to 90%.
Instead of facing the high costs of retooling or ordering large quantities, companies can print the precise number of parts required when they’re needed.
"By integrating 3D printing with a digital inventory, we can adopt a just-in-time production approach, which significantly reduces waste and excess stock,” adds Di Toto. “Not only does this lower storage costs, but it also aligns with our commitment to sustainability by minimising the environmental impact of our operations.”
A more sustainable practice
"3D printing promotes sustainability by enabling on-demand production, which reduces waste and the need for large inventories. This adaptability ensures that we can quickly respond to new challenges, making our operations more agile and efficient," explains Di Toto.
Francesco Pantaleone, chief business officer at Roboze, agrees that improved sustainability is key advantage of 3D printing.
“The ability to produce parts locally supports decentralised manufacturing, reducing dependency on global logistics and lowering carbon footprint,” Pantaleone says. “Furthermore, the ability to produce only what is needed, when it’s needed, plays a key role in minimising waste.”
While maintenance departments are the biggest users of 3D printing technology, its use has expanded into many areas of the rail industry, including technology development.
3D technology is particularly useful for prototyping, trialling new shapes and structures and exploring interfaces, tolerances and user experience, says Steve Carden, transport innovation expert at PA Consulting. He also points to the technology’s role in supporting training.
“3D replicas of rolling stock assets can be created, scaled in dimensions so that they can provide expanded views or so they’re more portable. These are then used in classrooms, rather than on the track, to provide a safer and more comprehensive training experience,” he explains.
What the future has in store
As the industry gains more experience with 3D printing, technologists anticipate broader adoption, including the production of more critical and safety-related components. They also expect the range of printable materials to expand further, to include new high-temperature and high-strength resins, which will unlock new applications.
Many organisations are already hard at work in this area – for example, Siemens is collaborating with universities and organisations including Deutsche Bahn, TUV Nord, and Lehvoss to develop new materials and processes for the faster approval of 3D printed safety critical parts.
Technologists also foresee increasing integration of 3D printing with predictive maintenance systems and digital twins, allowing rail operators to anticipate part failures and produce replacements before issues arise, optimising operational efficiency.
Don’t be afraid to ask ‘can this be printed’ the next time you’re looking for a solution.
Gavin John Lockyer, CEO of Arafura Resources
“In the future, we envision distributed 3D printing stations across rail networks becoming the norm, with decentralised digital supply chains driving greater responsiveness and innovation,” says Pantaleone.
For Hitachi, the opportunities that using 3D printing presents extend beyond replacement parts and into the new build area.
“We are exploring the use of 3D printing in the construction of new train units. This includes producing components that can be directly integrated into the assembly of new trains, taking advantage of the design flexibility and material capabilities offered by the 3D printing systems,” explains Di Toto.
“By incorporating 3D printed parts into new builds, we can optimise designs for performance, reduce the overall weight of the train, and improve energy efficiency. This approach also allows for a higher degree of customisation, meeting specific customer requirements and enhancing the overall passenger experience.”
Manufacturers like Alstom believe the sky is the limit as far as 3D printing is concerned, and Sandhu is excited to see what’s in store next. She concludes with this piece of advice to those working across the rail industry, whether in design, manufacture, or maintenance.
“Don’t be afraid to ask ‘can this be printed’ the next time you’re looking for a solution,” says Sandhu. “This is a relatively new technology for rail, but the possibilities are endless and here at Alstom we’re really excited about where it will take us in the future.”
The mine’s concentrator can produce around 240,000 tonnes of ore, including around 26,500 tonnes of rare earth oxides.
Gavin John Lockyer, CEO of Arafura Resources
Total annual production
Phillip Day. Credit: Scotgold Resources
Production challenges for rare earth supply chains
There are two key issues with the production of REEs. First, all the rare earth deposits are mixed together, so it is difficult and expensive for processors to separate them and to take advantage of their individual properties. It is similarly challenging to split up the more valuable ones, such as terbium, from those of little value, like lanthanum.
Second, REEs are bound up in mineral deposits with the low-level radioactive element, thorium, exposure to which has been linked to an increased risk of developing lung and pancreatic cancer.
These obstacles create a huge challenge for any Western company that wants to become involved in the industry. However, they must be overcome if the Western world is to end its dependence on China.
Caption. Credit:
The biggest rare earth mines are located in China, and this source of domestic production has helped drive Chinese dominance. The Bayan Obo deposit in Inner Mongolia, north China – containing 40 million tonnes of rare earths reserves – houses the world’s largest deposits. The mine has been in production since 1957 and currently accounts for more than 70% of China’s light REE production.
However, Western mines are aiming to change this balance of production and power. The Mountain Pass Mine, owned by MP Materials , a Las Vegas-based mining company, is an open-pit mine of rare earths on the south flank of the Clark Mountain Range, 85km south-west of Las Vegas. In 2020, the mine supplied 15.8% of the world’s rare earth production and is the only rare earth mining and processing facility in the US.
In October 2020, Donald Trump, the former US president, signed an executive order declaring a national emergency in the mining industry, aimed at boosting the domestic production of rare earths. Trump ordered his cabinet to study the matter, with a view towards giving government grants for production equipment and imposing tariffs, quotas or other import restrictions against China.
The move, it said, would “allow the US Government to leverage the resources of its closest allies to enrich US manufacturing and industrial base capabilities and increase the nation’s advantage in an environment of great competition”.
The move, it said, would “allow the US Government to leverage the resources of its closest allies to enrich US manufacturing and industrial base capabilities and increase the nation’s advantage in an environment of great competition”.