IN FOCUS Excellence Awards Interview
Sponsored by Greenbrier Maxion
Railway Technology Excellence Awards 2024: Greenbrier Maxion
Greenbrier Maxion is headquartered in Brazil and is a Category Award Winner in the 2024 Railway Technology Excellence Awards
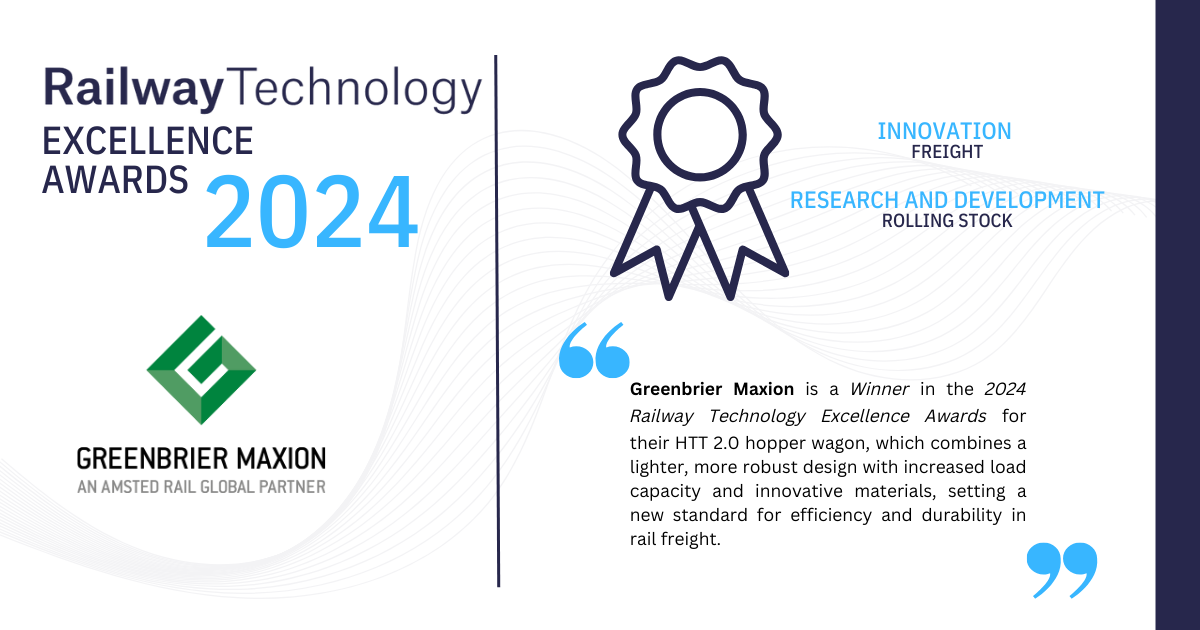
Greenbrier Maxion (GBMX), which has consistently demonstrated its commitment to advancing Brazil’s railway industry through innovation and strategic development, has won two awards in the 2024 Railway Technology Excellence Awards, in the Innovation and Research and Development (R&D) categories.
The Railway Technology Excellence Awards celebrate the greatest achievements and innovations in the railway industry. Powered by GlobalData’s business intelligence, the Awards recognise the people and companies that are driving change in the industry.
During 2022, the Group distributed 20,000 Dignity Kits into refugee camps and rural areas in more than five locations in the Middle East
Zarina Kanji, head of business development and marketing for TMall Global, Alibaba Group UK & Nordics.
GBMX won the R&D award for its HTT 2.0 hopper wagon, which is lighter yet more robust due to a redesigned concept and rigorous testing, and the Innovation award for enhancing load capacity by 4%, using new corrosion-resistant materials, and improving the draft sill design, leading to greater operational efficiency and fuel economy.
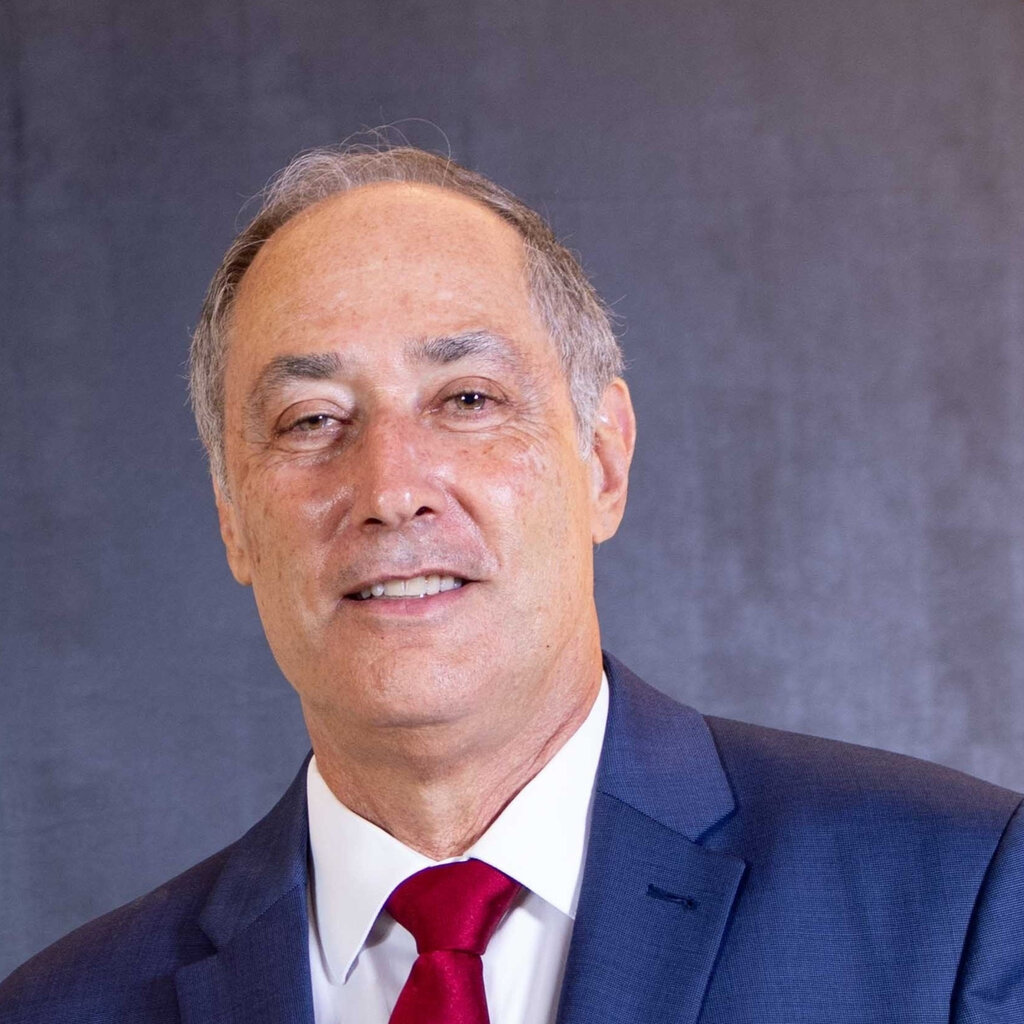
Eduardo Scolari, Greenbrier Maxion CEO
Eduardo Scolari, president of Greenbrier Maxion, the largest railway industry in South America, participated in an interview with GlobalData after winning the Excellence in Railway Technology 2024 award in the Innovation and Research and Development (R&D) categories.
Railway Technology: How do you ensure that Greenbrier Maxion stays at the forefront of innovation in the railway industry?
In recent years, we have been preparing our facilities to better meet the demands that are likely to arise in the coming years. We have invested heavily in automation and made many changes to our manufacturing facilities, incorporating plenty of technology and innovation.
By the way, automation is no longer just a question of productivity, as it was in the past. Skilled labour like ours is already hard to find in Europe and the US, which is why the priority is to retain talent through training, development, and appreciation.
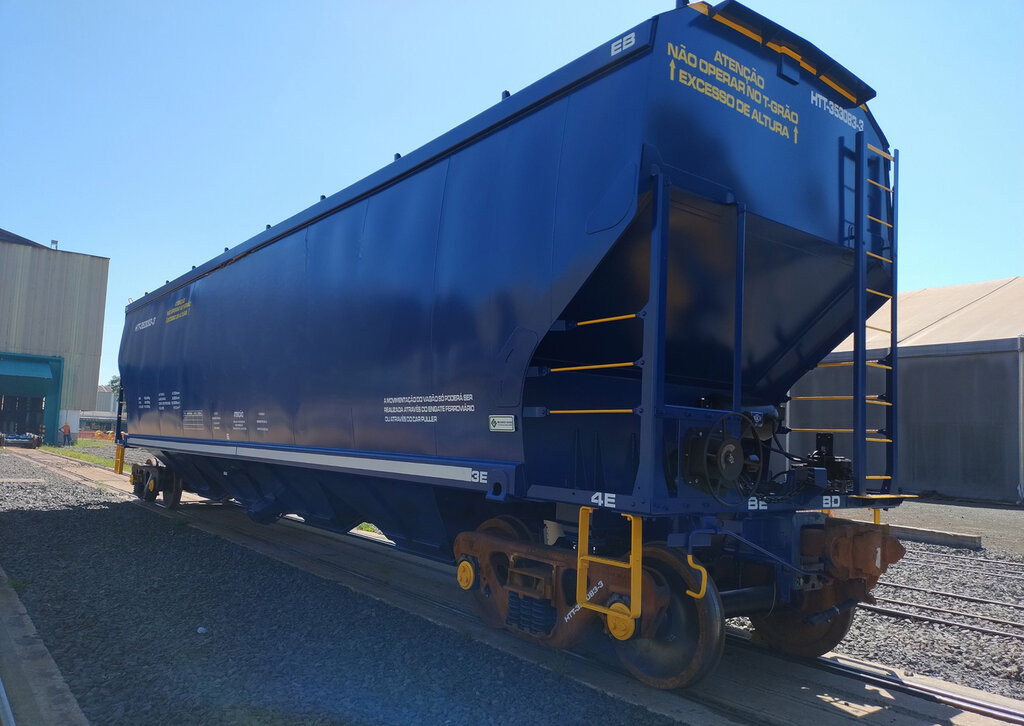
Caption. Credit:
Through this need, we have implemented important projects in the company that favour and qualify human capital, such as a welding School held on the company's facilities, with training and retraining courses for welders.
There is also Formare - a socio-educational project that promotes professional qualification courses for low-income young people. Implemented at Greenbrier Maxion 15 years ago, it trains professionals and citizens. It has served around 300 young people in Hortolândia-SP since its inauguration. We also operate SENAI's Apprentice Programme, developed in partnership with SENAI Sumaré, which develops young people aged 18-21 for their first professional experience, in an environment of constant learning.
We are attentive to all the changes and dynamism of the railway sector. We develop and produce all types of wagons using simultaneous assembly lines with robotised, modern, robust and precise processes. With a portfolio of more than 30 models, the wagons produced are designed to meet the needs of each customer, according to the cargo to be transported and the characteristics of each railroad.
With differentiated technology, the wagons have a reduced tare weight, greater load capacity, greater energy efficiency by reducing fuel consumption and pollutant emissions, reliability, easy loading, unloading and maintenance, thereby reducing logistics costs.
We build solutions that are always ahead of the needs of the model, thinking about how to make clients more profitable, more productive, safer and more efficient, in a sustainable way and together. The GBMX is ready with all the latest technology, and we have designed our products with the best in the world for railroads in Brazil, as well as developing robust and competitive national solutions. We are equipped with products, processes, and people.
Railway Technology: The HTT 2.0 hopper wagon represents a significant advancement in rolling stock design. What was the inspiration behind this project?
A project that is the result of GBMX's strategy of offering customers solutions that deliver real benefits, solve their problems and significantly help them achieve their goals.
The HTT 2.0 is an extremely strategic product for GBMX, which is responsible for transporting some of Brazil's main export products and has a significant share of the Brazilian rail market. As such, this model is constantly evolving technically, with constant monitoring of application conditions and customer service, which allows us to identify opportunities to offer improvements to the product and have value for our customers.
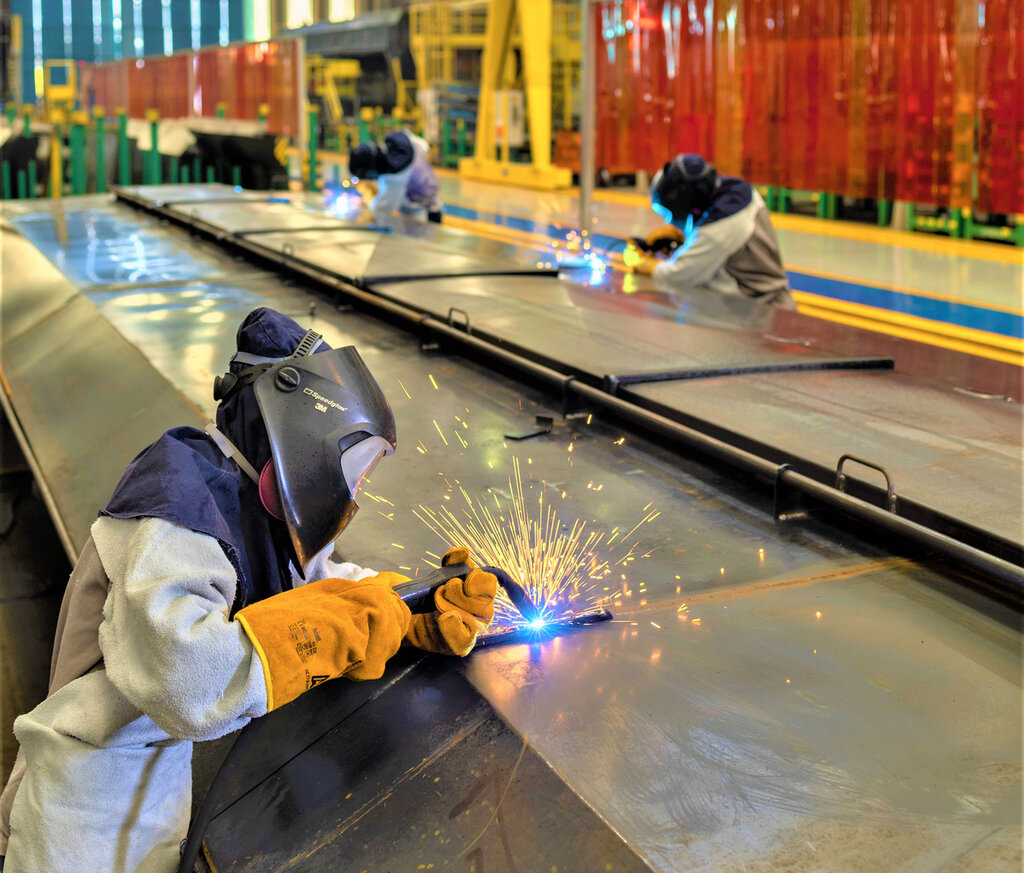
Caption. Credit:
In the case of HTT 2.0, the increase in the wagon's capacity was extremely significant and was only possible due to a robust engineering process, in which all of the client's operational characteristics were surveyed, analysed and used to prepare the project. Improvements like this, in addition to having value for the client in terms of economic viability, also generate extremely relevant attributes such as a reduction in polluting gas emissions, which strategically boosts rail transport in Brazil.
Railway Technology: Can you discuss the role of customer feedback in shaping the development of the HTT 2.0?
All GBMX projects are carried out with a focus on the client's needs and HTT 2.0 was no different. GBMX maintains a very close and transparent technical relationship with its clients, with a team dedicated to being present in the day-to-day operation, maintenance, and terminals with the main objective of identifying opportunities for products and services.
This relationship, which involves the client's effective participation in the development process, is essential to the success of the project. Especially in Brazil, where the railroads operate in isolation and with different characteristics, the relationship with each client allows us to identify specific opportunities for each application, which results in a competitive advantage for the GBMX product.
Railway Technology: How does GBMX approach the balance between increasing wagon capacity and maintaining safety standards?
Product development, aiming for innovation as the initial focus of any project, results in the evolution of the wagon in all its aspects, such as improvements in operation, maintenance, durability, reliability, and safety. Among the most important features, the reduction in the wagon's tare weight (unladen weight), the increase in load capacity, and improvements in transportation efficiency are real product gains.
In addition to gains in customer productivity, these improvements are directly related to the efficiency of the country's rail transportation and show significant advances in reducing fuel consumption and pollutant emissions. The new generation of wagons also provides safer operating conditions, with components that reduce the risk of derailment and enable an increase in operating speed.
GBMX has a very robust product development process that includes, in addition to all the main state-of-the-art engineering tools used in the design, a field test stage, with an instrumented prototype, where all the characteristics, especially those related to safety, are evaluated.
To summarise, all safety assumptions are considered during the design of the wagon through simulations with virtual tools, and although the Brazilian standard does not require validation in the field and in real operating conditions, GBMX adopts this stage as mandatory for all its new projects, which raises the level of safety.
Railway Technology: The use of polymer bushings and stainless steel pins is a notable innovation in the HTT 2.0. What prompted the shift to these materials?
In Brazil, as a strategic matter seeking maximum transportation efficiency within the operational and infrastructure conditions available, bulk carriers are designed to transport various products with different characteristics.
While in other countries there are specific wagon models for transporting each type of product, Brazilian railroads use the same model for sugar, soy and corn, which have different specific weights, for example.
Recently the demand for transporting highly corrosive fertilisers has increased significantly, and with greater exposure to this type of product, solutions using polymers and stainless steel have been adopted for greater product durability and reliability with these new operating conditions.
Railway Technology: How has the introduction of a pneumatic system for door operation improved the efficiency of bulk cargo transportation?
The use of pneumatic systems solves several problems faced by railroads in Brazil. The first, which is measurable, is related to the reduction in unloading time, which improves transportation efficiency. However, the project provides gains, not measurable at first, that are just as relevant, if not more so.
Replacing manual operation with automatic operation eliminates all the risks of accidents to operators that the conventional process brings. In addition, it eliminates the need for physical effort to open the wagon, eliminating issues related to time off work for ergonomic reasons.
Railway Technology: With the HTT 2.0, GBMX has achieved a reduction in tare weight. What impact does this have on the overall sustainability of rail transport?
The reduction in tare weight was, by far, the most challenging premise of this project. Change made in the project, through detailed studies and work by development engineering, led to a tare reduction of 700kg per wagon.
In other words, the new HT 2.0 is significantly more robust and lighter than the previous generation. All the benefits that HTT 2.0 delivers are based on solid, proven engineering work, utilising high-end tools and the most modern resources.
Increases in payload capacity and reductions in tare weight directly increase operational efficiency, defined here as the amount of cargo in metric tons transported per litre of diesel.
Comparing a train composed of 120 wagons from the old generation with another composed of 120 HTT 2.0 wagons during a typical bulk cargo operation in Brazil indicates that the train equipped with new generation hoppers could achieve a 2.4%-3.4% improvement in efficiency. This means it can transport more cargo using the same amount of diesel.
Railway Technology: How does GBMX's investment in high-end tools and modern resources translate into tangible benefits for your clients?
For many years, the evolution of wagons produced in Brazil was slow and driven by the market. However, there has been a reversal of the current logic, with the industry taking an active posture by investing in research and development with a focus on identifying and meeting customer needs and requirements.
This change in strategic orientation made it possible to deliver products with a high degree of technological evolution, which became the market standard. Product development aiming for innovation as the initial focus of any project results in the evolution of the wagon in all its aspects, such as improvements focused on operation, maintenance, durability, reliability, and safety.
Among the most important features, the reduction in the wagon's tare weight (unladen weight), the increase in load capacity, and improvements in transportation efficiency and terminals are real gains in products. In addition to gains in customer productivity, these improvements are directly related to the efficiency of the country's rail transportation and show significant advances in reducing fuel consumption and pollutant emissions.
The new generation of wagons also provides safer operating conditions, with components that reduce the risk of derailment and allow for an increase in operating speed.
Committed to sustainable development, there is a GBMX effort to ensure that the development of the wagons meets the value premises for customers and society that include the environmental, social, and economic areas, such as:
- increased productivity for the customer, allowing the transportation of a greater volume of cargo and resulting in a gain in competitiveness.
- increased energy efficiency resulting in reduced fuel consumption and consequently lower emissions of polluting gases.
- increased operator safety and ergonomics, guaranteeing the highest levels of working conditions.
- increased operational safety to reduce the risk of rail accidents, protecting people and property that interface with railroads.
- increased durability of components which leads to cost savings and more sustainable use of resources.
Another great differential of the GBMX wagons is the Motion Control® bogey - Premium Bogies, developed specifically for the operational and permanent way conditions of Brazilian railroads, providing through the optimisation of the dynamic behaviour of the wagon, a significant increase in operational safety and useful life of the components, as well as a reduction in maintenance costs.
Complementing the whole package of solutions, we also have a line specialising in rail services. Installed in a dedicated shed, it receives wagons in need of overhaul, maintenance, refurbishment, modernisation, and transformation of wagons and components, in a superior proposal in terms of benefits for the market.
Among the main advantages, the highlights are greater reliability and availability, better productivity, a reduction in maintenance backlogs, a reduction in indirect costs, materials management – and a reduction in train downtime, as well as the recycling and reuse of materials and parts.
Railway Technology: What strategies does GBMX employ to stay ahead of regulatory changes and industry standards?
GBMX constantly invests in research and development with a focus on identifying and meeting customer needs and requirements, as well as automating its production processes. This enables us to deliver products with a high degree of technological evolution, which has become the market standard and established the industry's positioning, consolidating its goal of pioneering the innovation process for wagons in Brazil.
In addition, the company relies on a network of knowledge and relationships that enable the updating and enhancement of crucial topics for the development of innovative solutions, both in product and service development, and in process improvement, as follows:
- companies of the Amsted Rail and Greenbrier group (stakeholders).
- global wagon and bogie manufacturers.
- associations and class entities to strengthen the industry and the rail modal, as well as being a reference in parameters and rules for the sector such as fleet renewal, wagons scrapping, the useful life of wagons, and components and revisions in clauses of current and new rail concessions:
- ABIFER - Brazilian Railway Industry Association.
- ABNT - Brazilian Association of Technical Standards.
- ANTF - National Association of Railway Transporters.
- ANTT - National Land Transport Agency.
- SAE - Society of Mobility Engineers.
- Partnerships with Universities and Research Institutes:
- IPT - Institute for Technological Research.
- UNICAMP - State University of Campinas.
- ITA - Technological Institute of Aeronautics.
- AAR - American Association of Railroads.
In terms of optimising production processes, we highlight the robotic welding cell on the assembly line, bringing innovation as a strategy, high quality and repeatability, better ergonomic and safety conditions for employees, and a reduction in hours per unit.
Today, GBMX has robot cells for welding sub-assemblies, many of which were developed internally by our automation engineering team. In addition to the robot cells, our teams have implemented automation on the assembly line, such as the closing device and the hopper wagon welding positioner – which has a total capacity of 30 tons – allowing height adjustment and the possibility of safety monitoring of the equipment and the work area. This resulted in a 42% reduction in the handling time of the positioner, which complies with Brazilian standards.
As a major innovation, we have implemented virtual reality for engineering, which provides an immersive experience for interacting with designs, allowing for the evaluation of maintainability, ergonomics, and safety, as well as more comprehensive and detailed design reviews, reducing costs and the time it takes to launch products on the market.
The painting simulatorhas also been implemented. This is a system that allows for painting training, bringing higher quality and reduced costs and volatile organic compound emissions. Soon, we will be implementing a welding simulator.
Railway Technology: Can you share how GBMX fosters a culture of innovation within the company?
Since 2020, Greenbrier Maxion has been working to develop initiatives aimed at promoting a culture of creativity and innovation, using the 4DX methodology (dour disciplines of execution), developed by Franklin Covey Consulting, which helps the teams to organise themselves and achieve their crucially important goals.
Every year, internal championships are held to engage all employees, with the directors and president sponsoring the teams. In each championship, the main goals for each team are implemented, unfolding into projects that include cost reduction and productivity gains, achieving excellent results.
Another constant practice is benchmarking with the group's companies around the world, such as the Greenbrier Companies and Amsted Rail, promoting project optimisations, technology exchange and new ideas and practices that can be incorporated in Brazil and GBMX teams.
Railway Technology: Looking beyond the HTT 2.0, what are the next challenges GBMX is aiming to tackle in the railway sector?
New technologies should emerge to make the process easier, but human capital will still be essential, and sustainability will be primordial and an indispensable item of competitiveness. An example from our segment is the Green Rail Fleet programme, which makes it possible to create a three-year plan, replacing obsolete wagons with modern ones, as well as prioritising safety.
The renovations approved must already induce operators to be more efficient and acquire rolling stock, not just to increase capacity, but to replace the inefficient assets that are in circulation. It must be emphasised that the new fleet will bring more efficiency and competitiveness to the railroads, and that end users and authorised companies will already benefit from acquiring more technological and innovative wagons. The ESG footprint is the future, and if we don't fit the model into these aspects, we will fall behind the market.
Currently, almost 50% of the Brazilian fleet is over 30 years old, with almost 24,300 of these wagons already over 50 years old and operating with low productivity. We defend a programme to be built between government, industry, and railroads, to renew the old fleet in the medium term, replacing wagons with obsolete technology with modern ones, as well as prioritising safety.
In addition, in recent years we have seen an increase in the purchase of wagons by railroad users, which was unusual, and has helped to maintain the industry over the last two years. For the next few years, we expect an increase in these new customers, who are increasingly looking to have their own fleet to transport their products.
In addition to hopper wagons, we have a line of tank wagons for transporting petroleum products, cement, and sulphuric acids; a line of gondola wagons for transporting iron ore, bauxite, and coal; a line of platform wagons for handling steel cargo and lined or stacked containers; and a line of FTT total siderwagons for transporting pulp. These demonstrate our flexibility, diversity, and competitiveness in producing wagons that meet the future demands and requirements of customers and end users of the railroad.
Railway Technology: How does GBMX envision the future of freight transportation?
Industry expectations are relatively optimistic. The federal government's programmes for renewing concessions, new auctions, and even the requests from authorised companies – the Pro-Rail Programme – lead us to believe that new requests could come in as early as 2025.
However, the results are not yet reflected in the industry, which has been idle for some time. We have a production capacity of 10,000 wagons per year and the figures are well below that. However, for the next few years, we are confident of an increase in demand. For 2024, we expect the early renewals of FCA and Rumo Malha Sul, the re-bidding of Rumo Malha Oeste and the concessions for Ferrogrão, FIOL II and III, and FICO I and II.
We are relatively optimistic about the Brazilian rail market for the coming years, especially with the government's plan to increase rail's share of transport to 40% by 2035. What we have seen is a great deal of interest, not only from operators but also from users, in expanding their logistics to the railroads.
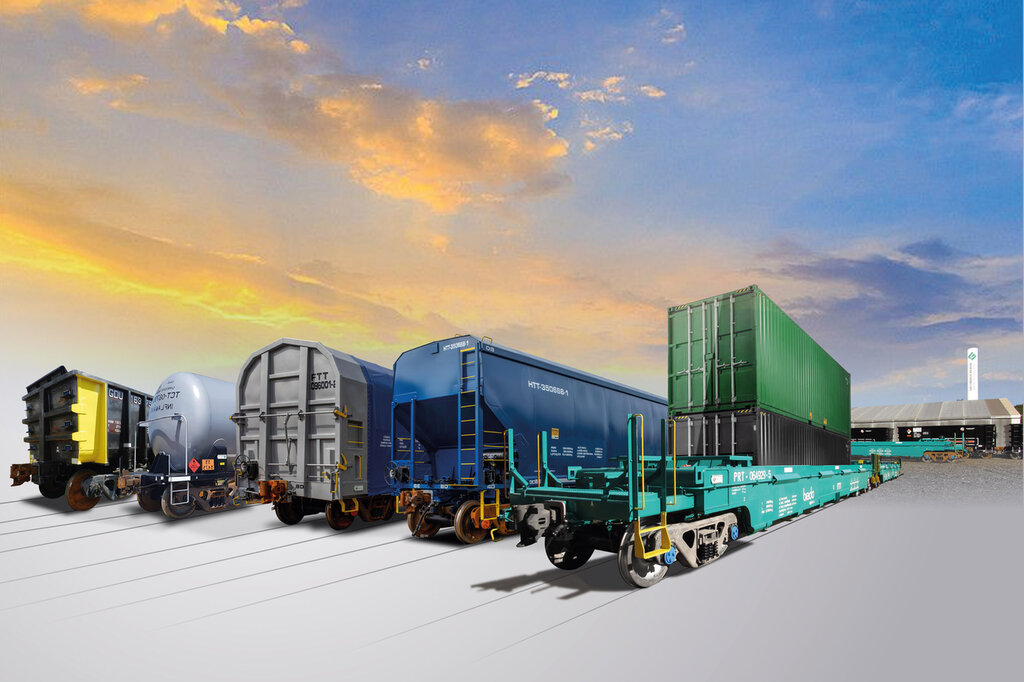
I believe that over the next few years, we will increasingly expand our operations with the use of innovative technologies in the development of wagons for the most diverse types of cargo. We have already been working on this and we have the know-how and technology to provide the railroads with the most modern equipment. I am sure that Greenbrier Maxion will continue to make history in the sector.
Potential projects and challenges for the future:
- A demand of 4,000 wagons per year would be the ideal minimum for the Brazilian industry and its supply chain to maintain a minimally adequate level of production.
- Government to speed up projects for renewals, concessions and authorisations.
- Rail freight also needs to be competitive (balancing the transportation matrix in Brazil).
- Today, the industry has all the technology that operators need, including international competitiveness. But these technologies, as well as not being replaced by the operators, come up against the logistical obstacles we have in terminals and ports. The whole cycle needs to be compatible.
- The increase in transportation seems effective, but the operators do not yet have the efficient, safe and sustainable rolling stock to meet this future.
- Prioritise the fight against social deprivation, while simultaneously expanding infrastructure, which is always a precursor to development, with combined solutions for the country's continued growth.
Company Profile
Originating from FNV (“National Wagon Factory”), Greenbrier Maxion is currently formed by the merger of the American companies The Greenbrier Companies and Amsted Rail Inc., as well as the Brazilian company Iochpe-Maxion. Located in Hortolândia-SP, it has been operating in Brazil for over 80 years and is considered the largest railroad industry in South America. It has affordable and efficient production capacity, with expertise in designing freight wagons, bogies, refurbishment services, adaptation and modernisation of wagons and their components.
GBMX wagons have a reduced tare weight, greater efficiency, reliability, increased load capacity, ease of loading and unloading and maintenance. Our rail bogies are produced using state-of-the-art technology to guarantee the best dynamic performance, an increase in the useful life of their components and a reduction in maintenance costs.
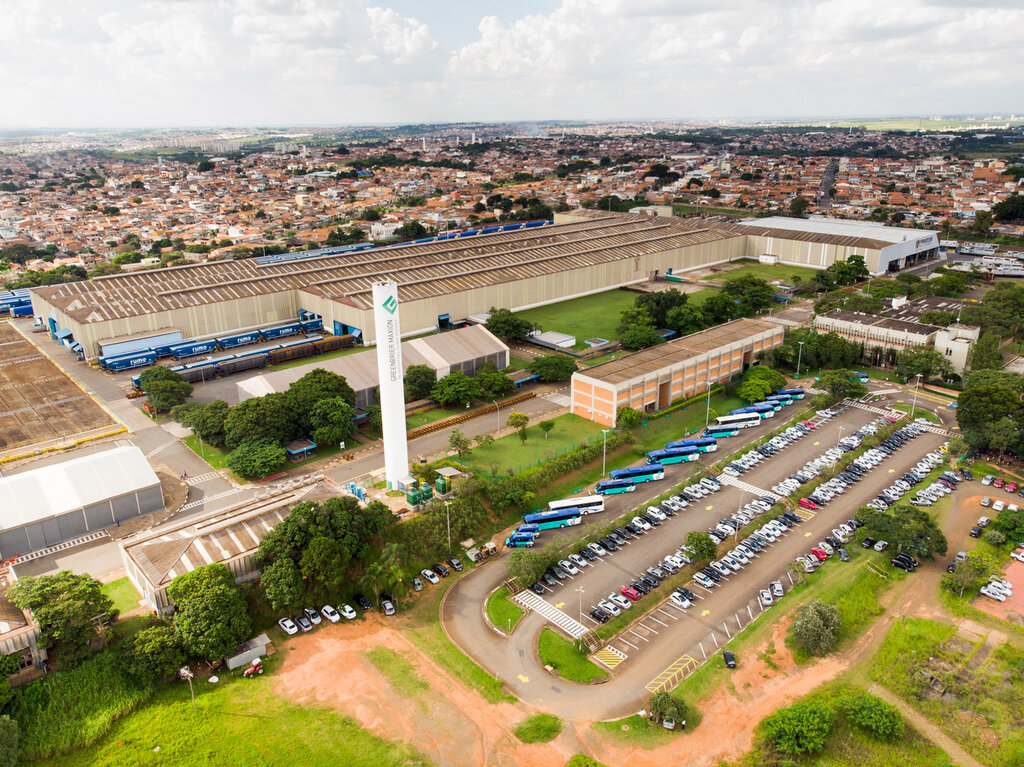
Caption. Credit:
Another highlight of Greenbrier Maxion is the line specialised in rail services, which receives wagons in need of overhaul, maintenance, refurbishment and transformation. This allows operators to concentrate their efforts on the focus of their business, reducing their maintenance worries. Find out more about Greenbrier Maxion at www.gbmx.com.br.
Eduardo Scolari
Eduardo Scolari is an executive with over 35 years of experience in large multinational companies. He has a degree in electronic and telecommunications engineering from the National Telecommunications Institute (INATEL) and participated in the IBM Business Management Institute educational programme. He holds a master’s degree in business administration from FGV University in Brazil and ISCTE in Portugal, with an extension in global business management. He is also certified in disruptive innovation by Harvard Business School.
He began his career in the Technology and Information sector at IBM. He has also worked at Flextronics and Dell Computers in Brazil. In December 2012, he joined AmstedMaxion as Operations Director, was promoted to Executive Operations Director in 2014 and since 2015 has held the position of President of Greenbrier Maxion.
In addition to his excellent relationship with industry associations, Eduardo is vice president of the Brazilian Railway Industry Association (ABIFER), a member of the American Chamber of Commerce and serves as a member of FIESP's Higher Council for Infrastructure (COINFRA).
“Greenbrier Maxion is today the largest railroad industry in South America and is prepared with the most innovative and modern technology to meet the demands of the railroad market, with differentiated projects for all types of cargo and railroads, with sustainability, quality, safety, and reliability.” - Eduardo Scolari, Greenbrier Maxion CEO
Contact information
Greenbrier Maxion
Avenida Carlos Roberto Prataviera, s/n Lote 71
Sítio São João, Jardim Nova Europa
Hortolândia | SP | CEP 13184-889
Web: www.gbmx.com.br
- Biffa internal savings data, average saving (January - August 2023)
- Nisbets internal savings data, average saving (January – September 2023)
- Compliance365 internal data, average savings
- HEINEKEN UK data, Calculations based on SmartDispense® active accounts each year since 2015 with 10 lines
- Independent test results based on subterranean and ground floor pub cellars of varying sizes
- Independent test results based on subterranean and ground floor pub cellars of varying sizes